精密壓鑄溫控利器-3D列印
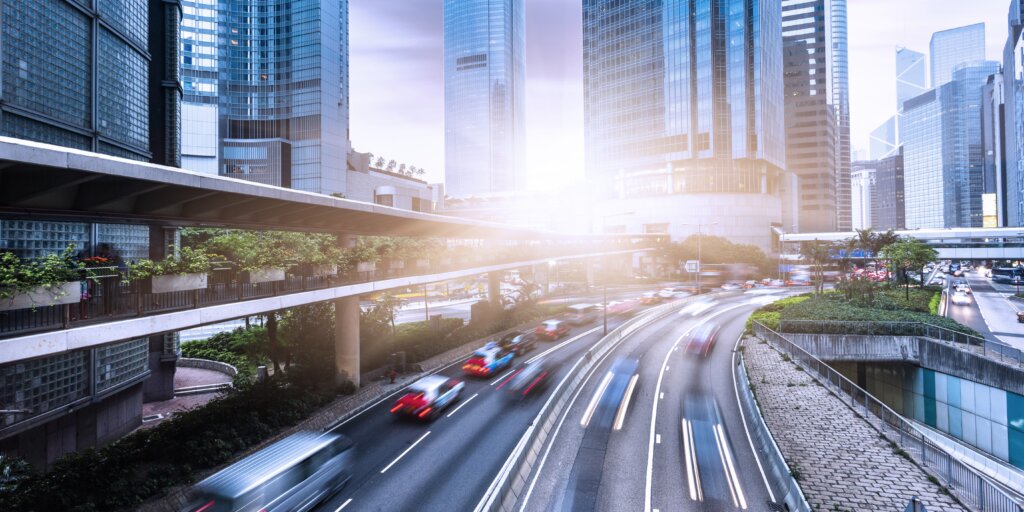
在環保和節能的大背景下,汽車製造、航空航太等行業對輕量化的需求越來越強烈。鋁合金,鎂合金成為實現輕量化的理想材料。特別是鋁合金因具有密度低、強度高的特性,在汽車零件製造中的應用不斷拓展。以汽車行業為例,歐洲鋁協發佈報告稱,到2030年歐洲乘用車,單車平均用鋁將達到 256kg。中國工信部《節能與新能源技術路線圖》提出,2025 年單車用鋁量目標為250kg/輛,2030年為 350kg/輛。汽車用鋁合金構件中,其中壓鑄鋁合金構件占比最高可達70%左右。從傳統燃油車動力傳動系統的缸體、缸蓋罩,變速箱殼體,轉向系統的鏈條蓋,到新能源汽車的電機殼體,電控系統以及一體化壓鑄車身構件,鋁合金壓鑄件的身影無所不在。
汽車行業反覆運算升級,新能源汽車產量不斷攀升,市場競爭加劇,更多的零件需要精密壓鑄成形技術來製造。特別是一體化壓鑄成型的出現,為壓鑄行業及壓鑄模具的發展帶來了新的機會和挑戰。其中,壓鑄件的良率及模具壽命的保證又是壓鑄廠及模具廠著重關注點及面臨的重要挑戰。壓鑄模具的整體熱平衡管理是突破這一挑戰關鍵的一環,其對模具的溫度分佈,應力控制,生產節拍和鑄件中縮孔 、開裂和鑄件表面品質等的管控起著重要作用。
特別是一體化壓鑄,鑄件重量較大形狀複雜,多數鑄件重量大於100kg,成型時熔融金屬釋放潛熱大,模具溫度變化錯綜複雜,模具各個部位溫度極不均勻。靠近澆口、澆道附近端模溫高,需要降溫散熱;產品壁厚較厚,模具難以散熱的熱點部位,需要重點降溫;模具末端模溫較低,需要合理控制熱量的散失,以免造成鑄件冷隔,注射不滿等缺陷。
目前主要以模溫機配合模具內部冷卻通道,分段控制模溫為主。受限於傳統冷卻通道的位置布局,模溫的控制不能完美匹配冷卻的需要。
3D打印技术能够制造出传统方法无法实现的优化冷却通道,该技术是实现模具热平衡管理的重要手段之一。3D打印技术制造出的带有异形水路的模具镶件,为压铸模具提供独特的竞争优势,在压铸领域应用越来越广泛。
3D打印的壓鑄模鑲件其特點是承受熱應力較大,內部冷卻通道設計複雜,因此對打印粉末的性能及冷卻通道的設計能力提出更高的要求。
目前較常見的3D列印粉末是1.2709(中國也稱18Ni300),是一種通用性麻氏體時效鋼材,成分特點是C(0.03%),Si(0.1%),Mn(0.15%),Cr(0.25%),Mo(4.5~5.2%),Ni(17~19%),Co(8.5~10%),Ti(0.8~1.2%)。在3D列印過程中,具有較好的列印成型性能,但在實際壓鑄生產應用中存在韌性不足,熱傳導性不佳,容易發生黏模等不良。前期使用過該粉末的客戶,不少反應過曾有早期開裂,不滿足生產預期的現象。
一勝百提供壓鑄模專用高性能3D打印粉末 – AM Dievar。
AM Dievar具有極佳的韌性,優異的高溫強度和熱傳導性,優秀的打印成型性,特別適合製造具有內部複雜冷卻通道的壓鑄模具鑲件。在對產品質量期望越來越高,生產效率提升,壓鑄成本不斷下降的驅使下,AM Dievar在面臨新挑戰的壓鑄行業中正在脫穎而出。
熱平衡管理的關鍵是模具內部冷卻通道的設計。一勝百對冷卻通道的設計秉承設計五部曲:
- 辨別模具中潛在問題區域;
- 根據基本的設計原則進行冷卻通道的設計;
- 模擬分析,如熱平衡分析、熱應力分析;
- 根據模擬分析結果,優化冷卻通道設計;
- 優化后再分析。
正是憑藉獨特的高性能壓鑄粉末及設計五部曲,一勝百的3D打印技術解決方案呈現出明顯的優勢,包括:
- 提高壓鑄件品質,降低廢品率:模具具有更均勻的溫度分佈,不存在局部熱點,壓鑄件壁厚較厚位置也能得到很好的冷卻,壓鑄件品質的一致性更好;
- 模具壽命更長:模具應力分佈得到優化,模具抵抗開裂的性能更佳,不會出現早期開裂現象;
- 降低維護需求:降低因模具損壞導致的停機和維護成本。
這些優勢在實際壓鑄生產應用案例中均有體現,如下是一勝百的3D打印技術解決方案的成功應用案例:
案例 1:
某大型壓鑄生產企業,在生產一款新能源汽車電控櫃時,壓鑄件局部面臨嚴重的粘著問題,產品表面品質不良,內部疏鬆導致產品氣密性不足。傳統模具製造技術無法有效解決此粘著問題,壓鑄生產過程中需要不斷停機,進行手工打磨,產品不良率居高。
經一勝百提供3D打印技術方案,使用AM Dievar打印的鑲件后,徹底避免原來每個班次都需進行手工打磨,提升產品良率5%以上,單件生產成本降低至原來的35%左右。
案例 2:
某汽車零件生產企業,在壓鑄生產一款發動機廢氣再循環系統零件時,因產品局部冷卻的需要曾採用過3D列印鑲件,鑲件約5-6萬模次便產生開裂現象,未達到企業生產預期的壽命。
一勝百經對模具進行分析,優化技術方案,採用AM Dievar打印的模具鑲件壽命提升40-50%,單件生產成本降低至原來的50%,且模具達成產品的生產批量需求。
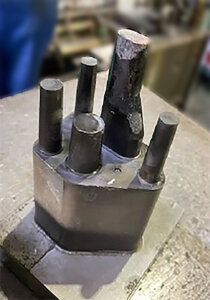
案例 3:
某壓鑄生產企業在生產一款發動機零件,產品批量大,品質要求穩定。 為達到縮短生產週期的目的,曾採用過3D列印1.2709製作分流錐,提升了生產效率。 但只生產約1.2萬模次,分流錐局部產生開裂,無法再繼續使用。
一勝百利用冷卻通道設計五部曲,優化冷卻通道的設計,並採用AM Dievar製作該分流錐,目前已經生產超過3.5萬模次,未發生失效且正常運作中。得益於AM Dievar較高的熱傳導性能,客戶的生產效率得到進一步提升。目前一勝百3D打印的AM Dievar分流錐在亞太地區已成功獲得客戶量產驗證,某一特定用戶AM Dievar分流錐壽命均達20萬以上。
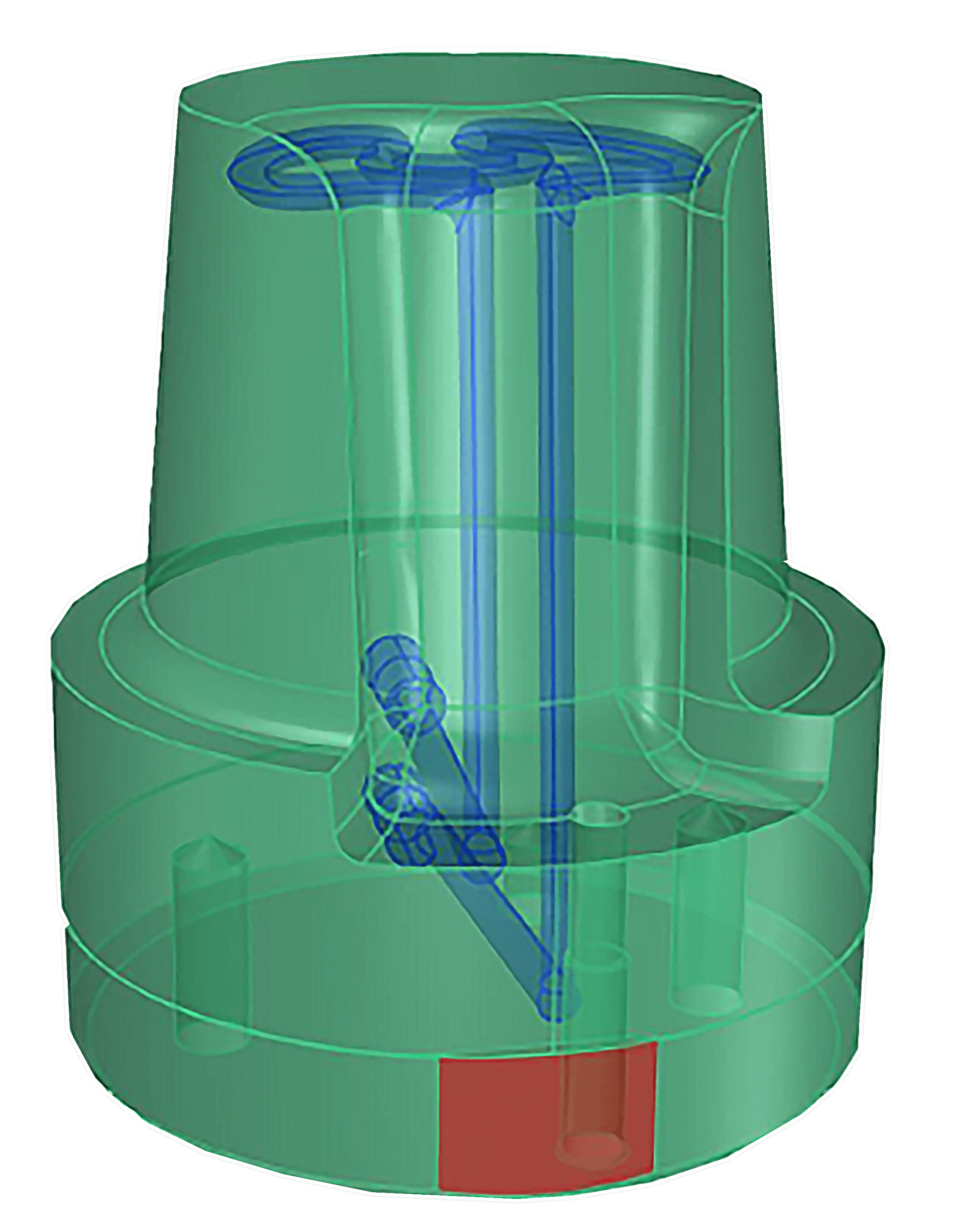
以上案例展示出一勝百3D打印技術解決方案在提升產品質量、生產效率,以及降低生產成本中的潛力。
同時3D打印技術創新的應用還可推動可持續發展,實現環境目標。
在一勝百成功應用的某一分流錐案例中,通過3D打印技術縮短生產周期10%,可實現減少12噸二氧化碳的排放。採用該技術,企業在保持競爭力的同時,也為環境保護做出貢獻。
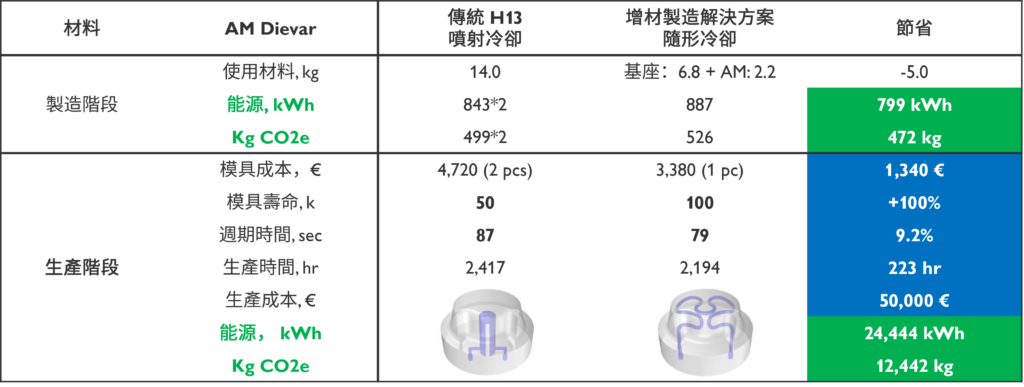
參考資料:
- 《一體化壓鑄給大型壓鑄模具製造帶來新契機》http://www.cqmjxh.cn/newsx.asp?id=1372&fid=6&lm=19
- 歐洲鋁協乘用車用鋁量研究與預測報告(2022-2030)_世鋁網
- 革命性壓鑄技術:通過3D打印,實現3000歐元投資轉化為45000歐元的年度節省