Optimalisasi Termal untuk Die Casting Menggunakan Teknologi Pencetakan 3D
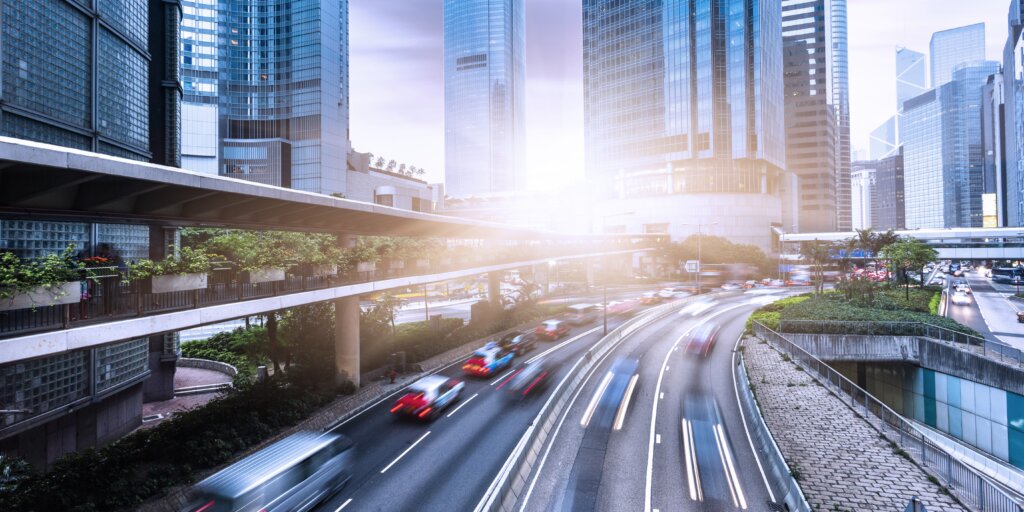
Dalam konteks perlindungan lingkungan dan penghematan energi, permintaan akan material yang ringan dalam produksi otomotif, kedirgantaraan, dan industri lainnya menjadi semakin kuat. Paduan aluminium dan magnesium telah menjadi material yang ideal untuk menghasilkan struktur yang ringan, terutama paduan aluminium, dengan karakteristik berat-jenis yang rendah dan kekuatan tinggi. Aplikasinya dalam pembuatan komponen otomotif terus berkembang. Sebagai contoh dalam industri otomotif, European Aluminium Association (Asosiasi Aluminium Eropa) melaporkan bahwa di tahun 2030, penggunaan aluminium per mobil penumpang di Eropa rata-rata akan mencapai 256 kg. ‘Pemetaan Teknologi Penghematan Energi dan Energi Baru’ dari Kementerian Perindustrian dan Teknologi Informasi Cina mengusulkan bahwa target penggunaan aluminium per mobil akan mencapai 250 kg di tahun 2025. dan 350 kg di tahun 2030. Dalam otomotif, proporsi komponen paduan aluminium yang diproduksi dengan die-casting bisa mencapai 70%. Mulai dari blok mesin, penutup kepala silinder, rumah transmisi dan penutup rantai sistem kemudi pada kendaraan bermesin pembakaran internal tradisional, hingga rumah motor, sistem kontrol elektronik, dan komponen bodi Mega-casting pada kendaraan energi baru, komponen die-casting paduan aluminium ada di mana-mana.
Industri otomotif sedang mengalami peningkatan terus menerus, dengan produksi kendaraan energi baru yang terus meningkat dan persaingan pasar yang semakin ketat. Semakin banyak komponen yang akan diproduksi menggunakan proses high pressure die-casting. Khususnya, pertumbuhan Mega-casting telah membawa peluang dan tantangan baru bagi pengembangan industri die-casting dan die making. Memastikan komponen die-casting berkualitas tinggi dan umur pakai die merupakan perhatian utama dan tantangan yang signifikan bagi die-maker dan die-caster. Manajemen keseimbangan termal die-casting secara keseluruhan merupakan faktor krusial dalam mengatasi tantangan ini, karena memainkan peran penting dalam mengontrol distribusi suhu die, kontrol tegangan, waktu siklus (cycle time) produksi, dan masalah produk, seperti porositas penyusutan, retakan, dan kualitas permukaan produk casting.
Khusus untuk Mega die-casting, pengecorannya relatif berat dan bentuknya rumit, dalam banyak kasus beratnya lebih dari 100 kg. Selama proses die-casting, logam cair melepaskan panas laten dalam jumlah besar, yang mengakibatkan perubahan suhu cetakan yang kompleks dan suhu yang sangat tidak merata di seluruh die. Suhu tinggi di dekat gate dan runner memerlukan pendinginan. Bagian dengan dinding produk yang tebal sangat panas dan memerlukan fokus khusus pada pendinginan. Sementara itu, suhu di ujung aliran logam relatif rendah, sehingga perlu mengendalikan kehilangan panas untuk menghindari cacat seperti penyumbatan (cold shuts) dan pengisian coran yang tidak memadai.
Saat ini, metode utamanya adalah menggunakan pengontrol suhu die yang dikombinasikan dengan saluran pendingin internal di dalam die untuk mengontrol suhu die di berbagai bagian yang berbeda. Namun, karena keterbatasan tata letak saluran pendingin tradisional, pengendalian suhu tidak dapat sepenuhnya memenuhi kebutuhan pendinginan.
Manufaktur Aditif (teknologi pencetakan 3D) mampu menciptakan saluran pendinginan optimal yang tidak mungkin dilakukan dengan metode tradisional. Teknologi ini merupakan salah satu cara penting untuk mencapai manajemen keseimbangan termal pada die. Insert die dengan saluran pendinginan kompleks yang dibuat dengan teknologi pencetakan 3D memberikan keunggulan kompetitif yang unik untuk cetakan die-casting, yang semakin banyak digunakan dalam industri die-casting.
Insert die-casting yang memerlukan pencetakan 3D biasanya mengalami tegangan termal yang tinggi dan memiliki desain saluran pendingin internal yang rumit. Oleh karena itu, tuntutan terhadap performa serbuk cetak (printing powder) dan kemampuan desain saluran pendingin menjadi tinggi.
Saat ini, serbuk cetak 3D yang umum digunakan adalah 1,2709 (juga dikenal sebagai 18Ni300 di Cina), yang merupakan baja maraging dengan dengan aplikasi serbaguna. Komposisi kimianya meliputi C (0,03%), Si (0,1%), Mn (0,15%), Cr (0,25%), Mo (4,5~5,2%), Ni (17-19%), Co (8,5~10%), dan Ti (0,8~1,2%). Meskipun memiliki kemampuan cetak yang baik, namun memiliki beberapa kendala seperti ketangguhan yang kurang, konduktivitas termal yang buruk, dan cenderung menempel pada die selama produksi die-casting. Banyak pelanggan yang telah menggunakan serbuk ini melaporkan keretakan dini dan kegagalan untuk memenuhi ekspektasi produksi.
ASSAB menawarkan serbuk Manufaktur Aditif (pencetakan 3D) berperforma tinggi khusus untuk cetakan die-casting – AM Dievar.
AM Dievar memiliki ketangguhan yang sangat baik, kekuatan termal dan konduktivitas termal yang unggul serta mampu-cetak (printability) yang tinggi, sehingga sangat cocok untuk insert cetakan die-casting dengan saluran pendinginan internal yang kompleks. Didorong oleh ekspektasi yang lebih tinggi terhadap kualitas produk, peningkatan efisiensi produksi, dan pengurangan biaya die-casting, AM Dievar unggul di industri die-casting untuk menghadapi tantangan baru.
Desain saluran pendingin internal merupakan kunci untuk manajemen keseimbangan termal pada proses die-casting. ASSAB mempraktikkan proses desain lima langkah untuk saluran pendingin:
- Mengidentifikasi area pada cetakan (die) yang berisiko mengalami kegagalan;
- Merancang saluran pendingin berdasarkan prinsip desain internal;
- Melakukan analisis simulasi, seperti analisis keseimbangan termal dan analisis tegangan termal;
- Mengoptimalkan desain saluran pendingin berdasarkan hasil simulasi di atas;
- Menganalisis lagi setelah optimalisasi.
Dengan mengandalkan serbuk cetak 3D berperforma tinggi yang unik – AM Dievar, dan pendekatan desain lima langkah, solusi ASSAB AM menunjukkan keunggulan yang jelas, termasuk:
- Meningkatkan kualitas komponen die-casting dan mengurangi tingkat scrap: Cetakan memiliki distribusi suhu yang lebih seragam, tanpa hot spot. Pendinginan yang efektif dapat dicapai pada bagian dinding yang lebih tebal pada bagian die-casting, menghasilkan konsistensi kualitas yang lebih baik.
- Umur pakai cetakan lebih lama: Distribusi tegangan pada cetakan dioptimalkan, meningkatkan ketahanannya terhadap retak dan mencegah masalah retak dini.
- Lebih sedikit perawatan: Mengurangi waktu henti dan biaya perawatan karena kegagalan cetakan.
Keunggulan ini tercermin dalam produksi die-casting. Berikut ini adalah beberapa kasus aplikasi solusi ASSAB AM yang berhasil:
kasus 1:
Sebuah perusahaan produksi die-casting besar menghadapi masalah soldering yang parah dengan die insert saat memproduksi kabinet kontrol listrik untuk kendaraan energi baru. Kualitas permukaan produk buruk dan porositas internal menyebabkan kegagalan uji kebocoran. Proses manufaktur die tradisional tidak dapat secara efektif menyelesaikan masalah soldering ini, sehingga menyebabkan seringnya terjadi gangguan untuk penggerindaan manual selama produksi die-casting karena tingkat skrap yang tinggi.
Setelah menerapkan solusi AM ASSAB dengan menggunakan insert printed AM Dievar, kebutuhan untuk penggerindaan manual di setiap shift benar-benar dihilangkan, sehingga meningkatkan tingkat-hasil (yield rate) lebih dari 5%, dan mengurangi biaya produksi sebesar 35% per komponen.
kasus 2:
Penyedia komponen otomotif menggunakan insert printed 3D dengan saluran pendingin konformal untuk mengurangi titik panas (hot spot) ketika melakukan die-casting komponen sistem resirkulasi gas buang mesin. Insert tersebut retak setelah 50.000 hingga 60.000 shots, sehingga tidak memenuhi umur pakai perkakas yang diharapkan.
ASSAB melakukan analisis pada die dan mengoptimalkan solusi teknis. Dengan menggunakan AM Dievar untuk mencetak insert die, umur pakai die meningkat 40-50%. Sebagai hasilnya, biaya produksi per komponen berkurang hingga 50% dibandingkan dengan menggunakan insert aslinya. Umur pakai insert die memenuhi persyaratan untuk seluruh batch produksi.
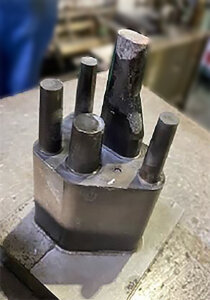
kasus 3:
Produsen die-casting memproduksi komponen mesin dengan jumlah besar dan persyaratan kualitas yang stabil. Untuk mempersingkat waktu siklus (cycle time) produksi, mereka menggunakan pencetakan (printing) 3D dengan serbuk AM tipe 1.2709 untuk memproduksi distributor, yang meningkatkan efisiensi produksi. Namun demikian, setelah hanya sekitar 12.000 shots, distributor tersebut retak dan tidak dapat digunakan lagi.
ASSAB mengoptimalkan desain saluran pendingin menggunakan proses desain lima langkah dan memproduksi distributor dengan AM Dievar. Kini distributor tersebut telah memproduksi lebih dari 35.000 shots dan masih berjalan tanpa mengalami kegagalan. Selain itu, efisiensi produksi juga semakin meningkat karena konduktivitas termal AM Dievar yang lebih tinggi dari 1.2709. Distributor yang dicetak menggunakan AM Dievar kini telah berhasil divalidasi untuk produksi massal oleh pelanggan di kawasan Asia-Pasifik. Untuk satu produsen tertentu, umur rata-rata distributor ini telah melampaui 200.000 shots.
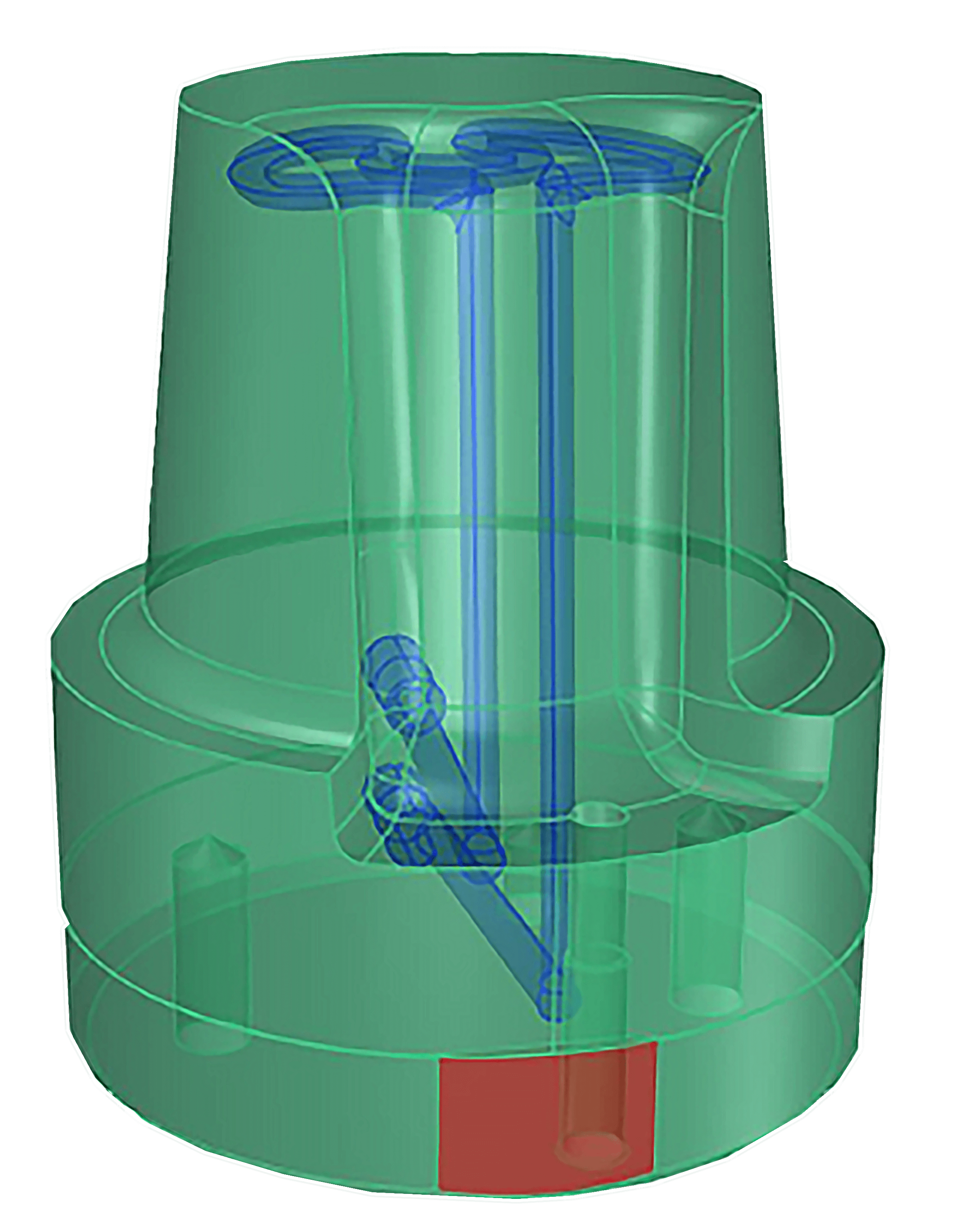
Kasus-kasus di atas menunjukkan potensi solusi AM ASSAB dalam meningkatkan kualitas produk dan efisiensi produksi, serta mengurangi biaya produksi.
Selain itu, aplikasi teknologi pencetakan 3D yang inovatif dapat mendorong pembangunan berkelanjutan dan mencapai tujuan lingkungan.
Selain itu, aplikasi teknologi pencetakan 3D yang inovatif dapat mendorong pembangunan berkelanjutan dan mencapai tujuan lingkungan. Dalam kasus aplikasi yang sukses dengan distributor die-casting, waktu siklus produksi berkurang 10% melalui teknologi pencetakan 3D dari ASSAB, sehingga menghasilkan pengurangan emisi karbon dioksida sebesar 12 ton. Dengan menerapkan teknologi ini, perusahaan dapat mempertahankan daya saing mereka sekaligus mendukung perlindungan lingkungan.
Perhitungan jejak karbon – Distributor
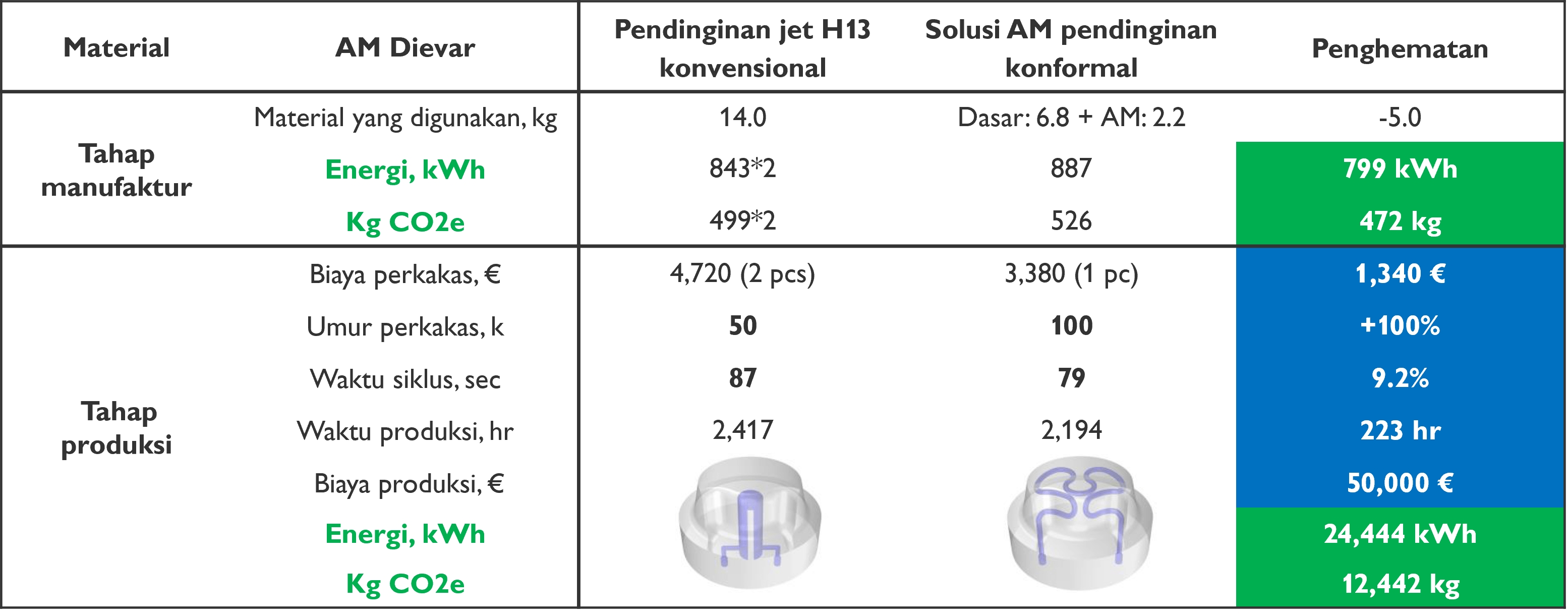
Reference
- Mega Die-Casting Brings New Opportunities for Large Die-Casting Mold Manufacturing, http://www.cqmjxh.cn/newsx.asp?id=1372&fid=6&lm=19
- European Aluminium Association Passenger Car Aluminium Usage Study and Forecast Report (2022-2030) – World Aluminium Network
- Revolutionary Die-Casting Technology: Achieving Annual Savings of €45,000 from a €3,000 Investment through 3D Printing