3D積層造形技術を用いたダイカストの熱管理の最適化
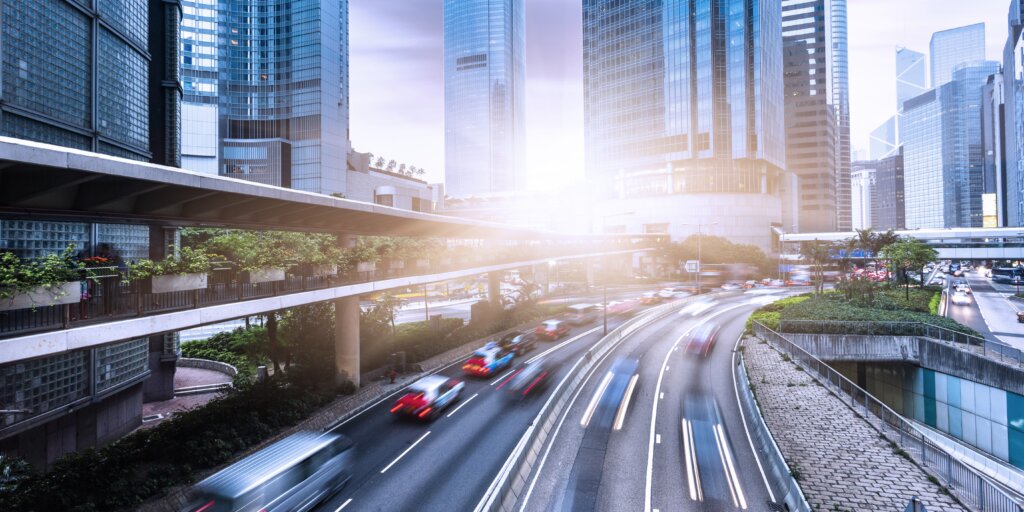
環境保護と省エネの点から、自動車、航空宇宙産業などにおける材料の軽量化への需要はますます高まっています。アルミニウム合金とマグネシウム合金は軽量構造を実現する最適な材料となっていますが、特にアルミニウム合金は低密度と高強度という特性を持つために注目されています。アルミニウム合金が自動車部品の製造に使われる事例は、引き続き増大しています。例えば、欧州アルミニウム協会の報告によると、自動車業界では2030年までに欧州の乗用車1台あたりの平均アルミニウム使用量は256kgに達するとされています。中国工業情報化部の「省エネおよび新エネルギー技術ロードマップ」では、1台あたりのアルミニウム使用量を2025年までに250kg、2030年までに350kgにするという目標を掲げています。自動車の場合、ダイカストを使ったアルミニウム合金部品の割合は70%に達する可能性があります。従来の内燃機関自動車のエンジンブロック、シリンダーヘッドカバー、トランスミッションハウジング、チェーンカバーから、新エネルギー車のモーターハウジング、電子制御システム、大型ダイカストボディ部品に至るまで、アルミ合金ダイカスト部品はさまざまなところに使われています。
新エネルギー車の生産量が引き続き増加し、市場競争が激化する自動車業界では、アップグレードが繰返し行われています。特に大型ダイカスト技術の採用により、多くの部品が高圧ダイカストを使用して製造されるようになり、ダイカスト業界と金型の展開に新たなチャンスと課題をもたらしています。特に、高品質のダイカスト部品と金型の工具寿命を保証することは、鋳造メーカーおよび金型メーカーにとって重要な懸念事項であり、大きな課題でもあります。この課題を克服する上でダイカスト用金型の全体的な熱バランスの管理が重要な要素になるのは、金型の温度分布、応力制御、生産サイクルタイム、鋳造製品の引け巣、亀裂、表面品質などの問題を管理する上で重要な役割を担うからです。
特に大型ダイカストの装置は、一般的に重く複雑な形状で、重量は100kgを超える場合がほとんどです。ダイカスト工程では、溶融金属から大量の潜熱が放出され、金型温度が複雑に変化し、金型全体の温度差が大きくなります。ゲートやランナー付近は高温になるため冷却が必要になります。製品の厚肉部は非常に高温になるため、特に冷却に留意する必要があります。一方、金属が流入する末端部の温度は比較的低く、鋳型の湯境や充填不足などの欠陥を避けるため、熱損失を抑制する必要があります。
現在、主な方法として、金型の温度管理と金型内の冷却回路を組み合わせて、異なる部位の温度を制御する手法が用いられています。しかし、従来の冷却回路の設計には限界があり、この温度制御では冷却のニーズを完全に満たすことはできません。
3D積層造形技術を用いると、従来の方法では不可能だった最適化された冷却回路の製造が可能です。この技術は、金型の熱バランスを効率的に管理する重要な方法の一つです。3D積層造形技術を用いて製造する複雑な冷却回路の金型入れ子は、固有の競争優位性があるため,ダイカスト業界でますます広く使われるようになってきています。
3D積層造形技術を必要とするダイカスト用入れ子には、通常、高い熱応力がかかり、内部の冷却回路の設計は複雑です。そのため、積層造形用粉末の性能と冷却回路の設計可能性には高い要求があります。
現在、3D積層造形用粉末として一般的に使用されているのは1.2709(中国では18Ni300とも呼ばれる)で、さまざまな用途に使用できるマルエージング鋼です。その化学組成は、C(0.03%)、Si(0.1%)、Mn(0.15%)、Cr(0.25%)、Mo(4.5~5.2%)、Ni(17~19%)、Co(8.5~10%)、Ti(0.8~1.2%)です。良好な造形性を発揮する一方で、十分な靭性が得られない、熱伝導率が低い、ダイカスト製造時に金型に凝着しやすいなどの問題があります。この粉末を使用した多くの顧客からは、早期の割れや期待する品質を下回るという報告があります。
ASSAB では、ダイカスト金型用に特化した高性能3D積層造形粉末、AM Dievar を揃えています。
AM Dievarは、優れた靭性、優れた高温強度、優れた熱伝導性、卓越した造形性を備えており、複雑な内部冷却回路のダイカスト金型入れ子に特に最適です。製品品質、生産効率の向上、生産コスト削減への高い期待に応えるAM Dievarは、新たな課題にも対応できるダイカスト業界で注目の材料です。
内部冷却回路の設計は、ダイカスト処理で課題となる熱バランスの管理に重要な要素です。ASSABは、次の5段階の冷却回路設計工程を採用しています。
- 金型の故障リスクの範囲を特定する。
- 金型内の設計原則に基づいて冷却回路を設計する。
- 熱バランスや熱応力解析などのシミュレーション解析を実施する。
- 上記のシミュレーション結果に基づいて冷却回路設計を最適化する。
- 最適化した後に再度解析を行う。
当社独自の高性能 3D 積層造形用粉末である AM Dievar と 5段階の設計工程を用いたASSAB AM ソリューションを利用すると、次の明確な利点が得られます。
- ダイカスト部品の品質の向上と不良品率の低減:金型の温度分布がより均一になり、ホットスポットの発生が抑えられます。ダイカスト部品の厚肉部の冷却が効果的にでき、安定した品質を維持できます。
- 金型寿命の延長:金型にかかる応力分布を最適化し、耐割れ性が向上し、早期に割れが生じる問題を防止できます。
- 補修頻度の低減:金型の故障によるダウンタイムと補修コストを削減できます。
これらの利点はダイカスト製造にも反映されています。以下は、ASSAB AMソリューションを用いた成功事例です。
事例 1:
大手ダイカストメーカーは、新エネルギー車の電気制御キャビネットを製造する際、金型入れ子の溶損に伴う深刻な問題を抱えていました。製品の表面品質が低く、内部に引け巣ができたためリークテストが不合格となりました。従来の金型製造プロセスでは、この溶損の問題の効果的な解決策がなく、不良率が高くなるため、ダイカスト生産中の手作業による研磨作業が頻繁に中断される原因となっていました。
ASSAB AM ソリューションを実行し、AM Dievar で積層造形した入れ子を使用した結果、各シフトでの手作業による研磨作業が完全に不要になり、製造工程の歩留まり率が 5% 以上改善され、部品あたりの生産コストを 35% 削減できました。
事例 2:
自動車部品メーカーは、エンジンの排ガス再循環システム部品のダイカスト製造時に生じるホットスポットを減らすため、コンフォーマル冷却回路のある3D積層造形入れ子を使用していました。この入れ子は、約5万~6万ショット後に割れが生じ、工具寿命の期待値を満たすことができませんでした。
ASSABは金型の分析を行い、技術面のソリューションを最適化しました。金型入れ子の積層造形にAM Dievarを使用したことで、金型寿命が40~50%向上しました。その結果、部品1個あたりの生産コストは、従来品を使用した場合と比較して50%削減されました。入れ子の寿命は、全体の生産バッチの要件を満たしました。
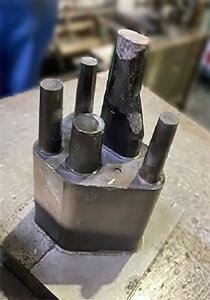
事例 3:
ダイカストメーカーは、安定した品質が求められるエンジン部品を大量生産していました。生産サイクルタイムを短縮するため、1.2709系AM粉末を使って3D積層造形で分流子を製造し、生産効率の向上を目指していました。しかし、わずか12,000ショットで分流子に割れが発生し、使用できなくなりました。
ASSABは、5段階からなる設計工程を用いて冷却回路設計を最適化し、AM Dievarを使って分流子を製造しました。この分流子は、現在までに35,000ショット以上を製造していますが、割れや故障は発生していません。AM Dievarの優れた高熱伝導性により、生産効率はさらに向上しました。AM Dievarを使用して積層造形した分流子は、アジア太平洋地域で大量生産に使用したお客様により効果が確認されています。一例では、この分流子の寿命が20万サイクルを超えたというメーカーもあります。
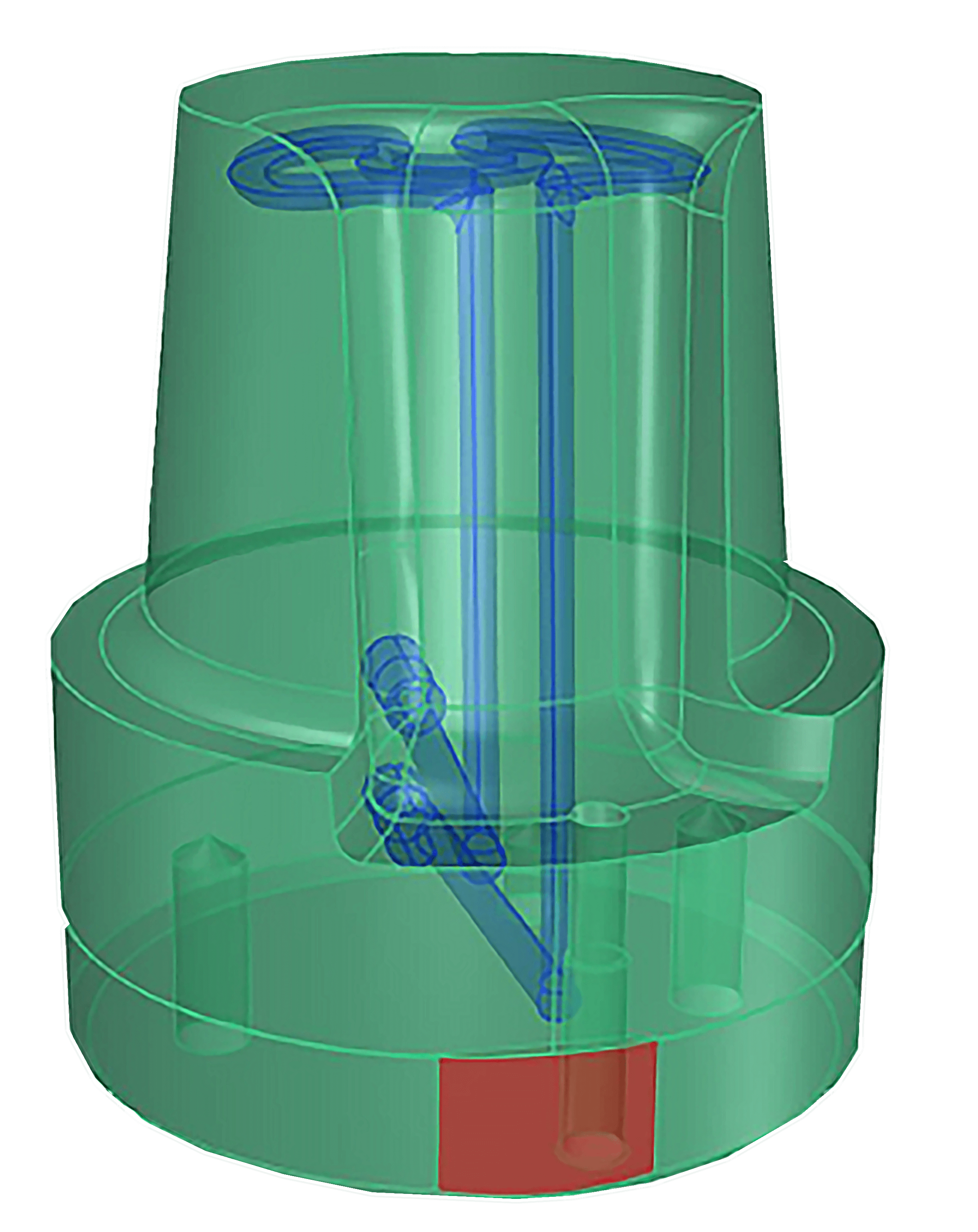
上記の事例から、ASSAB AMソリューションが製品品質と生産効率の向上、生産コストの削減に貢献する可能性があることがわかります。
さらに、3D積層造形技術を革新的に応用することで、持続可能な開発の促進、環境目標の達成にもつながります。
ダイカスト販売会社における成功事例では、ASSABの3D積層造形技術を活用した結果、生産サイクルタイムが10%短縮され、二酸化炭素排出量を12トン削減できました。この技術を導入することで、企業は競争力を維持しつつ環境保護にも貢献できます。
カーボンフットプリント計算 – 分流子
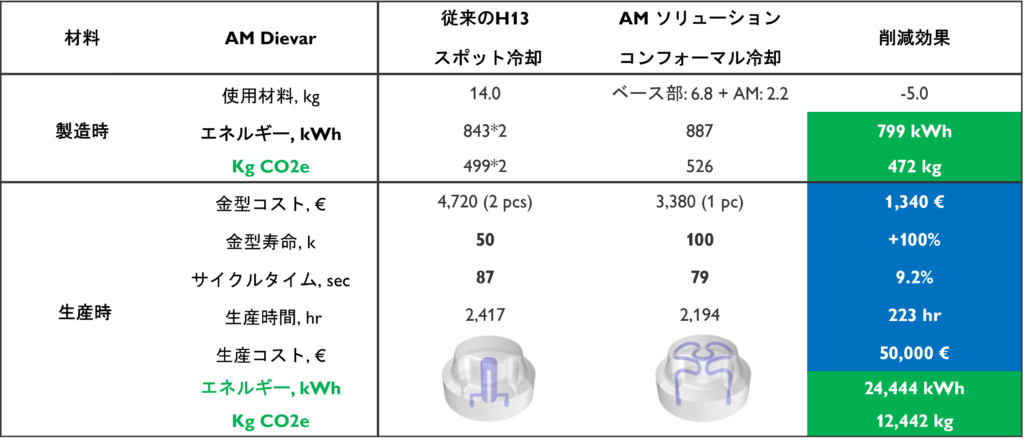
出典:
- Mega Die-Casting Brings New Opportunities for Large Die-Casting Mold Manufacturing, http://www.cqmjxh.cn/newsx.asp?id=1372&fid=6&lm=19
- European Aluminium Association Passenger Car Aluminium Usage Study and Forecast Report – World Aluminium Network
- Revolutionary Die-Casting Technology: Achieving Annual Savings of €45,000 from a €3,000 Investment through 3D Printing