Optimized Thermal Control for Die Casting Using 3D Printing Technology
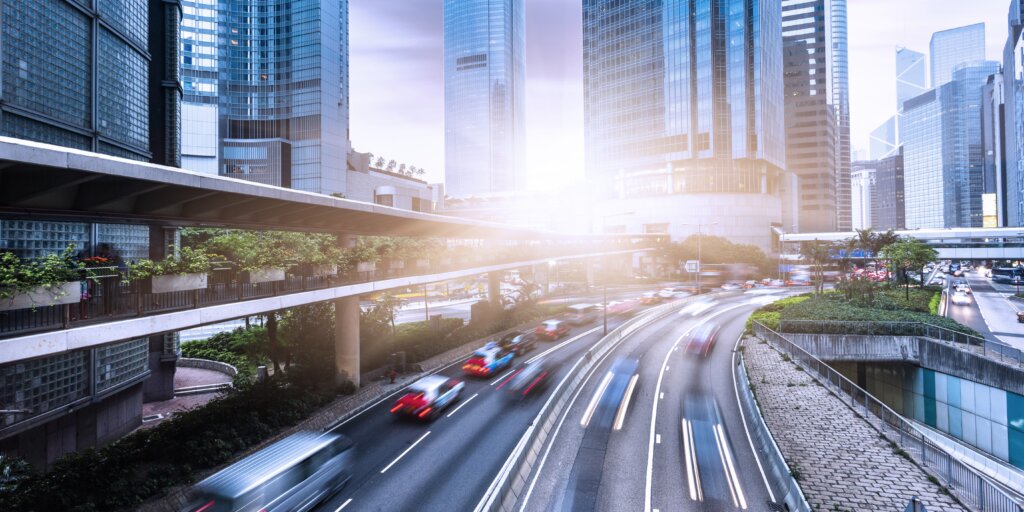
In the context of environmental protection and energy saving, the demand for lightweight materials in automotive manufacturing, aerospace, and other industries is becoming increasingly strong. Aluminum and magnesium alloys have become ideal materials for achieving lightweight structures, especially aluminum alloys, which are characterized by low density and high strength. Its application in manufacturing of automotive parts is continuously expanding. Taking the automotive industry as an example, the European Aluminium Association reports that by 2030, the average aluminum usage per passenger car in Europe will reach 256 kg. The Chinese Ministry of Industry and Information Technology’s ‘Energy Saving and New Energy Technology Roadmap’ proposes that the target for aluminum usage per car will be 250 kg by 2025 and 350 kg by 2030. In automotive, the proportion of aluminum alloy components manufactured by die-casting can be as high as 70%. From engine blocks, cylinder head covers, transmission housings, and steering system chain covers of traditional internal combustion engine vehicle, to motor housings, electronic control systems and Mega-casting body components of new energy vehicles, aluminum alloy die-casting parts are ubiquitous.
The automotive industry is undergoing iterative upgrades, with the production of new energy vehicles continuously increasing and market competition intensifying. More components are to be manufactured using high-pressure die-casting processes . Especially, the growth of Mega-casting has brought new opportunities and challenges to the development of die-casting and die making industry. In particular, ensuring high quality of die-casting parts and the die life are key concerns and significant challenges for die-casters and die manufacturers. Overall thermal balance management of die-casting dies is a crucial factor in overcoming these challenges, as it plays an important role in controlling die temperature distribution, stress control, production cycle time and product issues, such as shrinkage porosity, cracks and surface quality of the casting products.
Especially for Mega-casting, the castings are relatively heavy and complex in shape, weighing more than 100 kg in most cases. During die-casting process, the molten metal releases a large amount of latent heat, resulting in complex die temperature changes and highly uneven temperatures across the die. The temperature near the gate and runner is high, which needs cooling. The sections with thick walls of the product are very hot and require special focus on cooling. Meanwhile, the temperature at the end of the metal flow is relatively low, so it is necessary to control heat loss to avoid defects such as cold shuts and insufficient filling of the castings.
Currently, the main method is to use a die temperature controller combined with internal cooling channels within the die to control die temperature in different sections. However, due to the layout limitations of traditional cooling channels, temperature control cannot perfectly meet the needs of cooling.
Additive Manufacturing (3D printing technology) can create optimized cooling channels that are not possible in traditional methods. This technology is one of the important ways to achieve thermal balance management of dies. Die inserts with complex cooling channels made by 3D printing technology provide a unique competitive advantage for die-casting dies, which are increasingly used in the die-casting industry.
The die-casting inserts that require 3D printing are usually subjected to high thermal stress and have complex internal cooling channel designs. Hence, there are high demands on the performance of the printing powder and the design capability of cooling channels.
Currently, the commonly used 3D printing powder is 1.2709 (also known as 18Ni300 in China), a maraging steel with versatile applications. Its typical chemical composition includes C (0.03%), Si (0.1%), Mn (0.15%), Cr (0.25%), Mo (4.5~5.2%), Ni (17-19%), Co (8.5~10%), and Ti (0.8~1.2%). While it has good printability, if faces issues such as insufficient toughness, poor thermal conductivity, and a tendency to stick to the die during die-casting production. Many customers who have used this powder have reported early cracking and failure to meet production expectations.
ASSAB offers high-performance Additive Manufacturing (3D printing) powder specifically for die-casting dies – AM Dievar.
AM Dievar has excellent toughness, superior thermal strength, thermal conductivity and outstanding printability, making it particularly suitable for die-casting die inserts with complex internal cooling channels. Driven by higher expectations for product quality, production efficiency improvement and die-casting cost reduction, AM Dievar stands out in the die-casting industry to meet new challenges.
The design of internal cooling channels is key to thermal balance management in the die-casting process. ASSAB adheres to a five-step design process for cooling channels:
- Identify areas in the die with a risk of failure;
- Design cooling channels based on internal design principles;
- Perform simulation analyses, such as thermal balance and thermal stress analysis;
- Optimize the cooling channel design based on the above simulation results;
- Analyze again after optimization.
Relying on its unique high-performance 3D printing powder – AM Dievar, and the five-step design approach, ASSAB AM solutions show clear advantages, including:
- Improve the quality of die-casting parts and reduce scrap rate: The die has a more uniform temperature distribution without hot spots. Effective cooling can be achieved in the thicker-wall sections of the die-casting part, resulting in better quality consistency.
- Longer die life: The stress distribution of the die is optimized, improving its crack resistance to prevent early cracking issues.
- Less maintenance: Reduce downtime and maintenance costs due to die failure.
These advantages have been reflected in die-casting production. Below are some successful application cases of ASSAB AM solutions:
Case 1:
A large die-casting production company faced severe soldering issues with die inserts when producing an electric control cabinet for a new energy vehicle. The surface quality of the product was poor, and the internal porosity led to failure of leak test. Traditional die manufacturing processes could not effectively solve this soldering problem, which cause frequent interruptions for manual grinding during die-casting production, due to high scrap rate.
After implementing ASSAB AM solutions using AM Dievar printed inserts, the need for manual grinding in each shift was completely eliminated, improving yield rate by more than 5%, and reducing the production cost by 35% per part.
Case 2:
An automotive parts provider used 3D printed inserts with conformal cooling channels to reduce hot spots when die-casting an engine exhaust gas recirculation system component. The inserts cracked after 50,000 to 60,000 shots, failing to meet the expected tool life.
ASSAB conducted an analysis on the die and optimized the technical solution. By using AM Dievar for printing the die inserts, the die life increased by 40-50%. Consequently, the production cost per part was reduced to 50% compared to using the original inserts. The tool life of the insert met the requirement for the entire production batch.
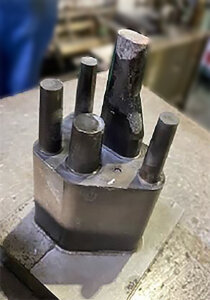
Case 3:
A die-casting manufacturer was producing an engine component with large batch and stable quality requirements. To shorten the production cycle time, they used 3D printing with 1.2709 type AM powder to manufacture the distributor, which improved the production efficiency. However, after only about 12,000 shots, the distributor cracked and could no longer be used.
ASSAB optimized the cooling channel design using the five-step design process and produced the distributor with AM Dievar. It has now been in production for over 35,000 shots and is still running without any failure. Moreover, the production efficiency has also been further improved due to higher thermal conductivity of AM Dievar than that of 1.2709. Distributors printed using AM Dievar have now been successfully validated for mass production by customers in the Asia-Pacific region. For one particular manufacturer, the average lifespan of these distributors has exceeded 200,000 shots.
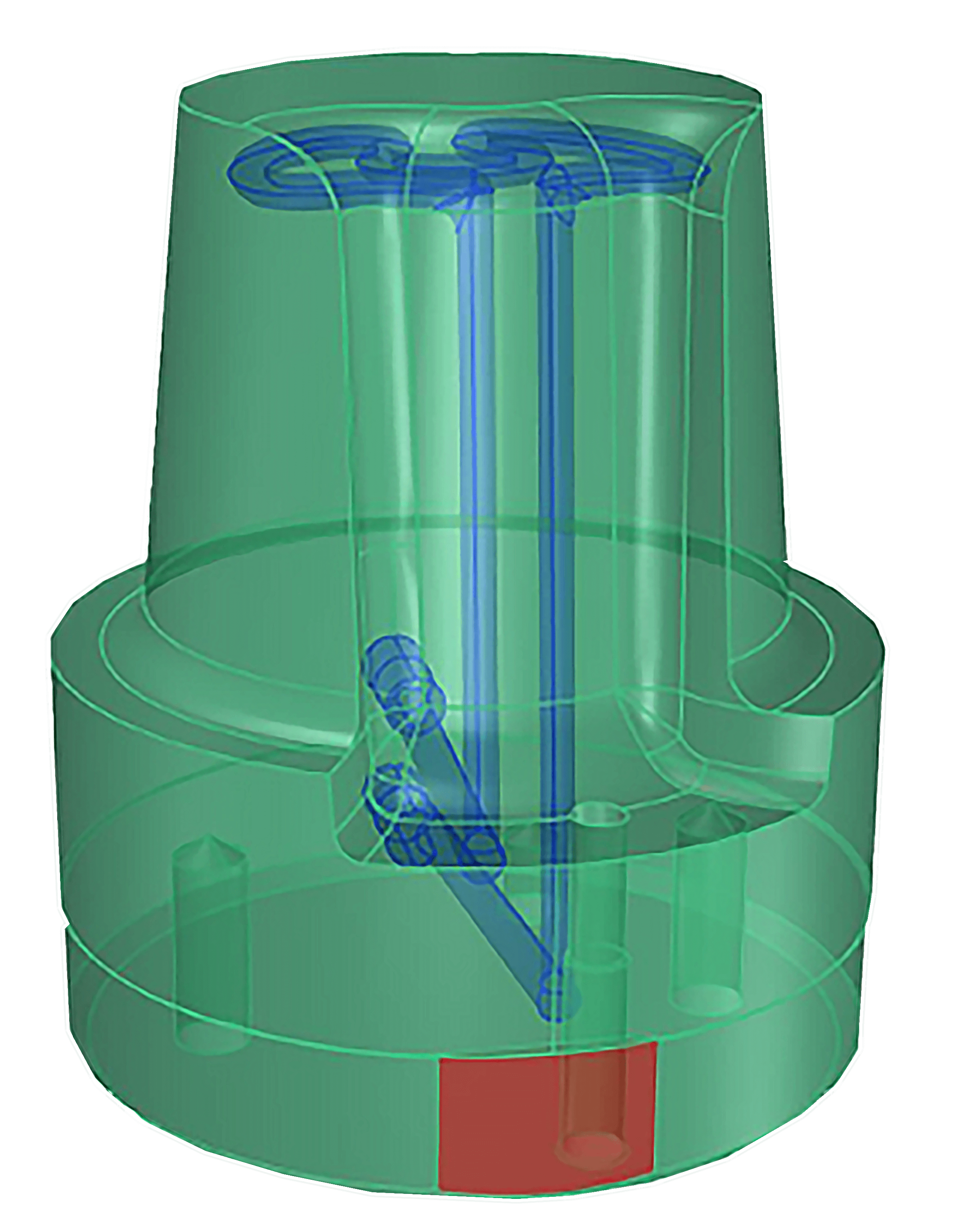
The above cases demonstrate the potential of ASSAB AM solutions in improving product quality and production efficiency, as well as reducing production costs.
Additionally, the innovative application of 3D printing technology can promote sustainable development and achieve environmental goals.
In a successful application case with a die-casting distributor, the production cycle time was reduced by 10% through 3D printing technology from ASSAB, resulting in a reduction of 12 tons in carbon dioxide emissions. By implementing this technology, companies can maintain their competitiveness while also supporting environmental protection.
Carbon footprint calculation – Distributor
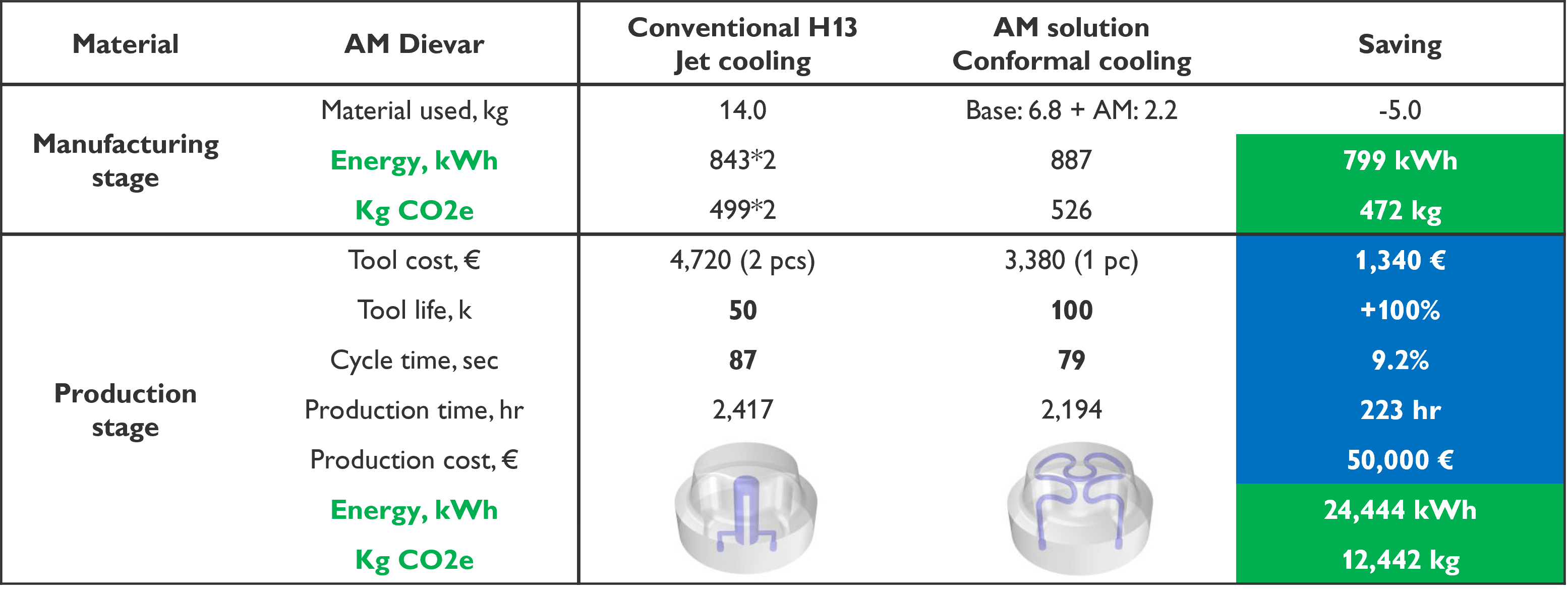
Reference
- Mega Die-Casting Brings New Opportunities for Large Die-Casting Mold Manufacturing, http://www.cqmjxh.cn/newsx.asp?id=1372&fid=6&lm=19
- European Aluminium Association Passenger Car Aluminium Usage Study and Forecast Report (2022-2030) – World Aluminium Network
- Revolutionary Die-Casting Technology: Achieving Annual Savings of €45,000 from a €3,000 Investment through 3D Printing