The suitable die material for the Automotive
Aluminum high pressure die casting has revolutionized the automotive industry by providing lightweight, durable, and complex components. Its versatility, cost-effectiveness, and production efficiency make it a preferred choice for automotive manufacturers aiming to improve vehicle performance through fuel efficiency while meeting strict quality and safety standards.
ASSAB offers a range of high performance die material solutions to fulfill your expectation and achieve a cost effective production with high repeatability.
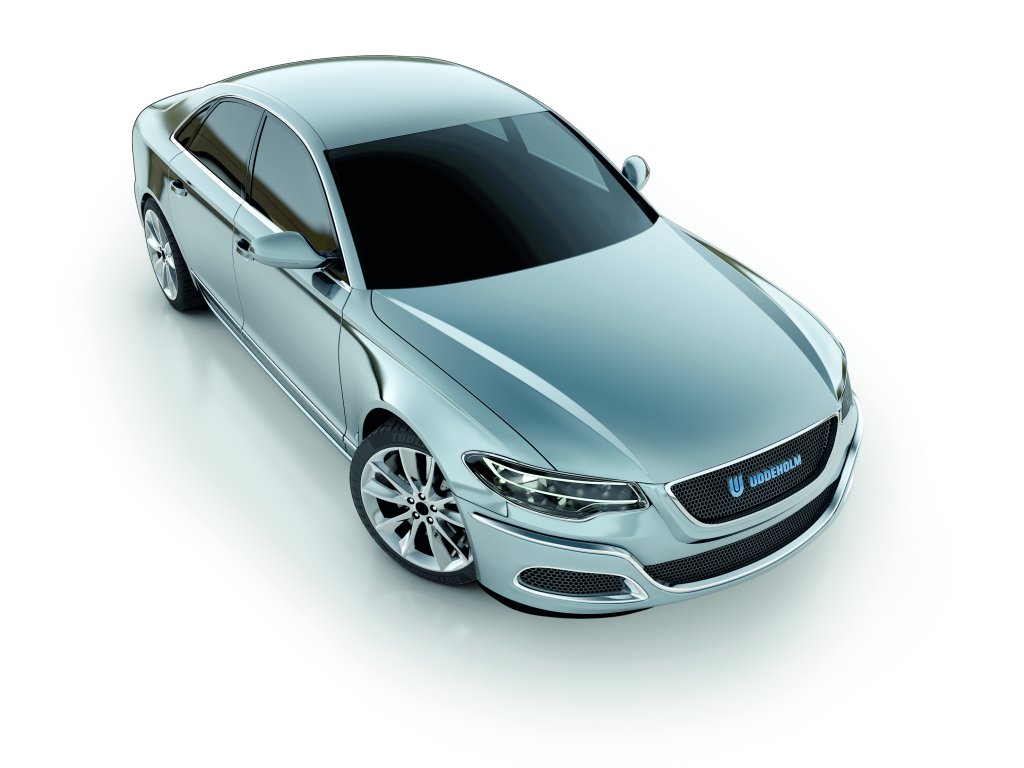
Choosing the right die steel for aluminum high-pressure die casting in the automotive industry is essential to ensure the production of high-quality, dimensionally accurate, and durable components. The experience from ASSAB as a die steel supplier helps you to select the most suitable die steel grade for your specific requirements.
In automotive high pressure die casting, the performance of die steel is crucial to achieve high quality and consistent results. Here are some key aspects of die steel performance in automotive high-pressure die casting:
Thermal Fatigue Resistance
The cyclic heating and cooling during the casting process leads to thermal stresses in the die steel causing fatigue cracks. Die steel with good thermal fatigue resistance can withstand the thermal stresses without cracking or deforming, ensuring prolonged tool life.
Toughness and Impact Resistance
Die steel should exhibit good toughness and impact resistance to withstand the thermal stresses from crack propagation and premature failure.
Heat Resistance
The die steel must possess excellent heat resistance to withstand the high temperatures encountered during the casting process. It should maintain its strength, hardness, and dimensional stability at elevated temperatures, ensuring prolonged die life and consistent casting quality.
The surface finish of the die steel is critical for achieving high-quality castings. Die steel with good properties to delay thermal fatigue helps to produce smooth and defect-free cast components without surface flaws formed by cracks hence minimizing post-processing requirements.
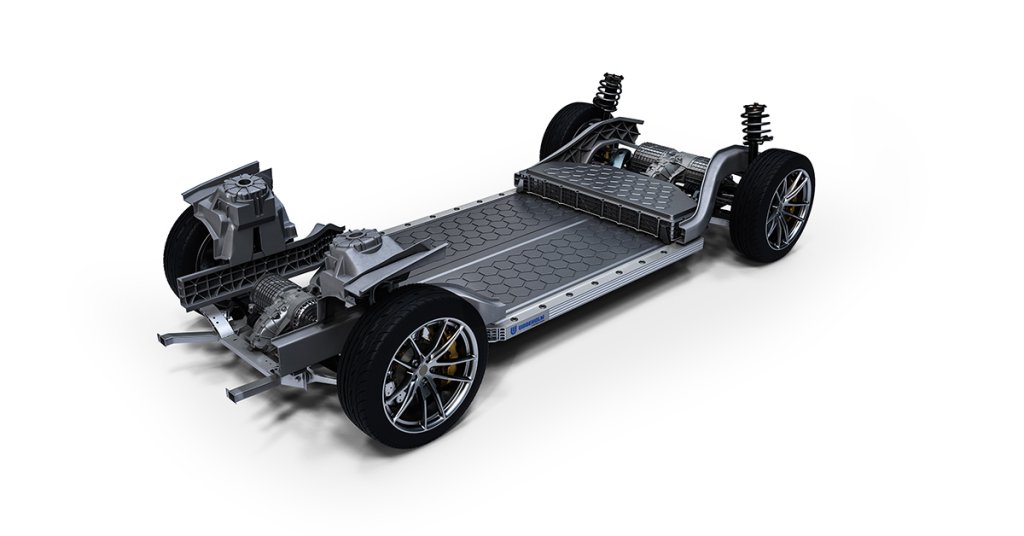
Dievar
Dievar is made for high performance high pressure die casting dies. The material properties of high impact toughness and heat resistance ensure high potential to delay thermal fatigue and therefore ensures consistent die performance.
Die steel should be chosen with consideration for maintenance and repair. Regular cleaning, polishing, and repairing of surface defects or cracks are essential for extending the lifespan of the die steel and maintaining casting quality. Dievar is friendly to weld repair with custom made weld rods of the same material for safe and consistent repairing.
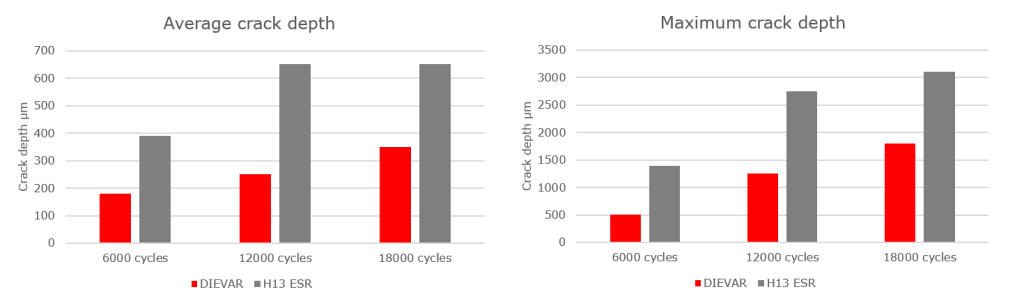
AM DIEVAR
AM Dievar inserts are increasingly being used in high-pressure die casting processes to enhance productivity, improve part quality, increase die life and enable design flexibility. These inserts, made using 3D printing techniques, offer several advantages in high-pressure die casting applications:
AM Dievar is utilized for the fabrication of intricate and complex geometries that pose challenges or are unachievable using conventional manufacturing methods. It enables the design of complex internal cooling channels that enhance the die performance and improve the solidification process during casting.
By incorporating conformal cooling channels within the AM inserts, heat transfer during the casting process can be significantly enhanced. Optimized cooling channels can help in reducing soldering formation, cycle times, improving part quality and minimizing the risk of defects such as shrinkage porosity in hot spot regions.
Additive manufacturing allows for rapid production of AM inserts compared to traditional machining methods. This reduces lead times and enables faster tooling iterations, facilitating faster product development cycles, time-to-market for new automotive components and prototyping.
Surface damage or wear can be repaired through localized additive processes such as laser metal deposition, reducing the need for complete replacement of die inserts.
Different AM technologies offer a wide range of materials suitable for die casting applications, including various metals and alloys. These materials can be selected based on their thermal properties, wear resistance, and compatibility with the casting material, ensuring optimal performance and longevity of the inserts.
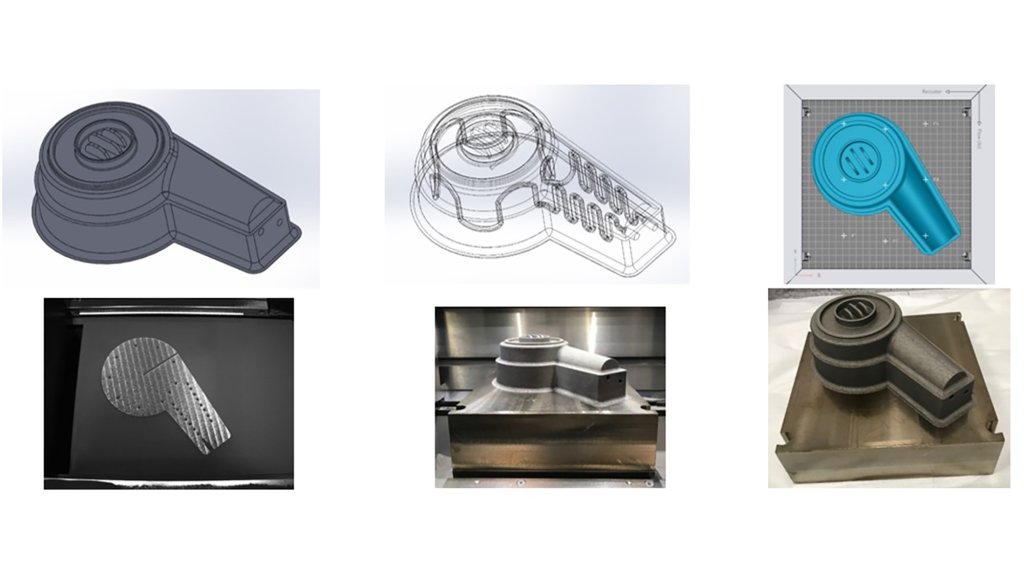
Please contact us for ASSAB solutions for the Automotive.