Blanking
Research in recent years has revealed a close relationship between failure mechanisms and tool steel properties. So when choosing right steel grades, especially for cold work tool steel, it helps to look at the failure mechanisms.
AUSTENITIC STAINLESS STEEL
The most common problem with blanking austenitic stainless steel is adhesive wear, chipping and galling. Initially, the material is soft and thus prone to adhere to the tool surface; but as it hardens during forming, this causes high stresses and may lead to chipping and cracking. Production lot size, thickness of plates and sheets are also important factors when choosing tool steel grades. These problems can be reduced by choosing materials that are resistant to adhesive wear and chipping.
SuperClean powder steel like Vanadis 4 Extra SuperClean, Vanadis 8 SuperClean and Vancron SuperClean are especially good for long runs. ASSAB 88, Caldie and Calmax are more appropriate grades for medium to short runs.
ADVANCED HIGH STRENGTH STEEL (AHSS)
The hardness and tensile strength of advanced high strength steel requires tooling materials with resistance against high wear, and chipping and cracking. These requirements are even more important with the ultra high strength steel, martensitic grades used today, which calls for tooling materials with multi-resistant profiles.
For superior performance for blanking high and ultra high strength sheets, choose ASSAB powder steels like Vanadis 4 Extra SuperClean, Vanadis 8 SuperClean or Vancron 40 SuperClean. Modern grades like ASSAB 88 and Caldie also yield significantly better performance than the traditional cold work steel.
MILD CARBON STEEL
Blanking soft carbon steel is prone to a varied range failure mechanisms. Some influencing factors are production lot sizes, steel thickness and complexity of the part being produced. Most types of steel can be used for blanking mild carbon steel but the governing factor in tool steel selection is total production costs.
With the increase of the thickness of the work material, the risk of chipping increases. The risk of local welding between the tool and the work material also increases causing adhesive wear and galling. Ejecting the punch may cause cracks as the ejecting force increases with the thickness. Opt for tool steel with a high degree of cleanliness and well distributed carbides in a homogenous matrix like the SuperClean powder steels.
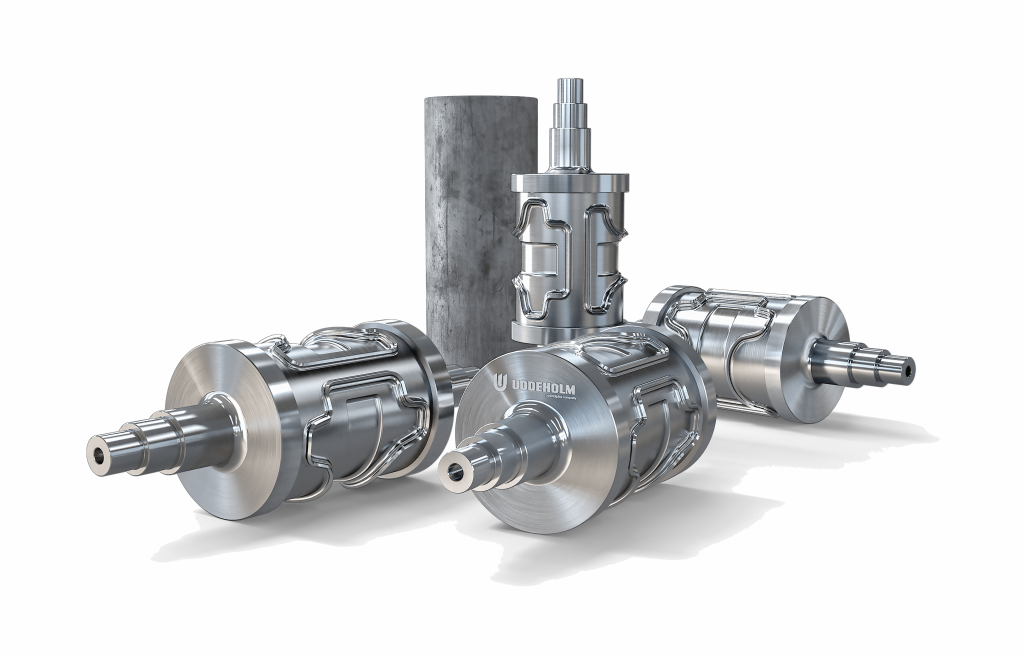