Kiểm Soát Nhiệt Độ Tối Ưu Cho Khuôn Đúc Bằng Công Nghệ in 3D
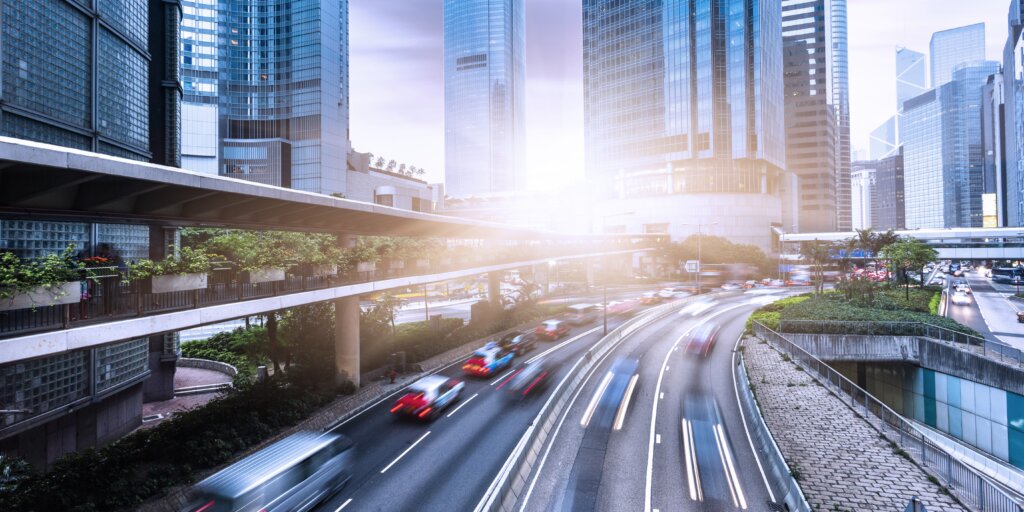
Trong bối cảnh bảo vệ môi trường và tiết kiệm năng lượng, nhu cầu về vật liệu nhẹ trong sản xuất ôtô, hàng không , và các ngành công nghiệp khác đang ngày càng trở nên mạnh mẽ. Hợp kim nhôm và magie đã trở thành vật liệu lý tưởng để tạo ra các cấu trúc nhẹ, đặc biệt là hợp kim nhôm, chúng có đặc điểm là trọng lượng nhẹ và độ bền cao. Ứng dụng của hợp kim nhôm trong sản xuất phụ tùng ôtô đang ngày càng mở rộng. Lấy ngành công nghiệp ôtô làm ví dụ, Hiệp Hội Nhôm Châu Âu báo cáo rằng đến năm 2030, lượng nhôm trung bình sử dụng cho mỗi chiếc ôtô chở khách ở Châu Âu sẽ đạt 256 kg. ‘Lộ Trình Tiết Kiệm Năng Lượng và Công Nghệ Năng Lượng Mới’ của Bộ Công Nghiệp và Công Nghệ Thông Tin của Trung Quốc đề xuất mục tiêu sử dụng nhôm cho mỗi ôtô sẽ đạt 250 kg vào năm 2025 và 350 kg vào năm 2030. Trong ngành ôtô, tỉ lệ các linh kiện hợp kim nhôm được sản xuất bằng phương pháp đúc áp lực có thể lên đến 70%. Từ khối động cơ, nắp đầu xi-lanh, vỏ hộp số, và nắp xích hệ thống lái của xe động cơ đốt trong truyền thống, đến vỏ động cơ, hệ thống điều khiển điện tử và các bộ phận thân xe đúc nguyên khối (mega-casting) của xe năng lượng mới – các chi tiết đúc bằng hợp kim nhôm hiện diện ở hầu khắp các cấu trúc xe.
Ngành công nghiệp ôtô đang trải qua quá trình nâng cấp liên tục với sản lượng xe năng lượng mới không ngừng tăng lên và sự cạnh tranh trên thị trường ngày càng gay gắt. Nhiều linh kiện đòi hỏi các quy trình đúc áp lực cao để sản xuất, đặc biệt là khi áp dụng công nghệ khuôn đúc Giga. Điều này đã mang lại những cơ hội và thách thức mới cho sự phát triển của ngành đúc áp lực và chế tạo khuôn. Trong đó, việc đảm bảo chất lượng cao cho các chi tiết đúc và kéo dài tuổi thọ khuôn là những mối quan tâm then chốt và cũng là thách thức lớn đối với các nhà sản xuất khuôn và sủ dụng khuôn. Việc kiểm soát cân bằng nhiệt tổng thể của khuôn đúc là một yếu tố cốt lõi để vượt qua những thách thức này vì nó đóng vai trò quan trọng trong việc kiểm soát sự phân bổ nhiệt độ của khuôn, kiểm soát ứng suất, thời gian chu kỳ sản xuất và các vấn đề về sản phẩm chẳng hạn như độ co ngót, nứt và chất lượng bề mặt của sản phẩm đúc.
Đặc biệt là đối với kỹ thuật đúc Giga, các sản phẩm đúc tương đối nặng và có hình dạng phức tạp, trong hầu hết các trường hợp, trọng lượng lên đến hơn 100 kg. Trong quá trình đúc, kim loại nóng chảy giải phóng một lượng lớn nhiệt ẩn, dẫn đến những thay đổi nhiệt độ khuôn phức tạp và sự phân bố nhiệt độ không đồng đều trên toàn bộ khuôn. Nhiệt độ khu vực gần cửa phun và kênh dẫn rất cao, cần phải được làm mát. Các phần có thành dày của sản phẩm rất nóng và yêu cầu tập trung đặc biệt vào việc làm mát. Trong khi đó,
Đặc biệt là đối với kỹ thuật đúc Giga, các sản phẩm đúc tương đối nặng và có hình dạng phức tạp, trong hầu hết các trường hợp, trọng lượng lên đến hơn 100 kg. Trong quá trình đúc, kim loại nóng chảy giải phóng một lượng lớn nhiệt ẩn, dẫn đến những thay đổi nhiệt độ khuôn phức tạp và sự phân bố nhiệt độ không đồng đều trên toàn bộ khuôn. Nhiệt độ khu vực gần cửa phun và kênh dẫn rất cao, cần phải được làm mát. Các phần có thành dày của sản phẩm rất nóng và yêu cầu tập trung đặc biệt vào việc làm mát. Trong khi đó, nhiệt độ ở cuối dòng chảy kim loại tương đối thấp, nên cần kiểm soát tình trạng mất nhiệt để tránh các khiếm khuyết như hiện tượng hàn nguội (không liền khối) và rót nguyên liệu không đủ vào chi tiết đúc.
Hiện nay, phương pháp chính là sử dụng một bộ điều khiển nhiệt độ khuôn kết hợp với các kênh làm mát bên trong khuôn để kiểm soát nhiệt độ khuôn ở các phần khác nhau. Tuy nhiên, do hạn chế về việc bố trí các kênh làm mát truyền thống nên việc kiểm soát nhiệt độ vẫn chưa thể thể đáp ứng hoàn hảo nhu cầu làm mát.
Công Nghệ Sản Xuất Phương Pháp in 3D có thể tạo ra các kênh làm mát được tối ưu hóa mà các phương pháp truyền thống không thể thực hiện được. Công nghệ này là một trong những cách quan trọng để đạt được khả năng kiểm soát cân bằng nhiệt của khuôn. Lòng khuôn có các kênh làm mát phức tạp được tạo ra bằng công nghệ in 3D mang lại một lợi thế cạnh tranh có một không hai cho khuôn đúc, nó ngày càng được sử dụng nhiều trong ngành đúc.
Các lòng khuôn cần in 3D thường phải chịu ứng suất nhiệt cao và có thiết kế kênh làm mát bên trong phức tạp. Do đó, thị trường xuất hiện các yêu cầu cao về hiệu suất của bột in và khả năng thiết kế kênh làm mát.
Hiện nay, bột kim loại để in 3D thường được sử dụng phổ biến là 1.2709 (còn được gọi là 18Ni300 ở Trung Quốc), thuộc nhóm thép maraging có những ứng dụng đa dạng. Thành phần hóa học của nó bao gồm C (0,03%), Si (0,1%), Mn (0,15%), Cr (0,25%), Mo (4,5~5,2%), Ni (17-19%), Co (8,5 ~ 10%), và Ti (0,8 ~ 1,2%). Tuy có khả năng in tốt, nhưng vật liệu này gặp các vấn đề như độ dẻo dai kém, độ dẫn nhiệt kém, và có xu hướng dính vào khuôn trong quá trình đúc. Nhiều khách hàng sử dụng loại bột này đã phản ánh xảy ra tình trạng nứt sớm và không đáp ứng được kỳ vọng về sản lượng.
ASSAB cung cấp bột kim loại để in 3D hiệu suất cao dành riêng cho khuôn đúc – Bột kim loại AM Dievar.
Bột kim loại AM Dievar sở hữu độ dẻo dai tuyệt vời, khả năng chịu nhiệt vượt trội, dẫn nhiệt tốt và khả năng in ấn xuất sắc, đặc biệt thích hợp cho các lõi khuôn đúc yêu cầu thiết kế hệ thống kênh làm mát phức tạp bên trong. Dưới áp lực kỳ vọng ngày càng cao về chất lượng sản phẩm, cải thiện hiệu quả sản xuất và giảm chi phí đúc khuôn, AM Dievar đã khẳng định vị thế vượt trội trong ngành đúc để đáp ứng những thách thức mới.
Thiết kế hệ thống kênh làm mát bên trong khuôn là chìa khóa để kiểm soát cân bằng nhiệt trong quá trình đúc khuôn. ASSAB áp dụng quy trình thiết kế kênh làm mát gồm năm bước:
- Xác định các khu vực trong khuôn có nguy cơ hư hỏng;
- Thiết kế hệ thống kênh làm mát dựa trên các nguyên tắc thiết kế bên trong;
- Thực hiện phân tích mô phỏng, chẳng hạn như cân bằng nhiệt và phân tích ứng suất nhiệt;
- Tối ưu hóa thiết kế kênh làm mát dựa trên kết quả mô phỏng bên trên;
- Tiến hành phân tích lại sau khi tối ưu hóa.
Dựa vào bột in 3D hiệu suất cao độc nhất – AM Dievar, cùng với quy trình thiết kế năm bước, Giải Pháp Sản Xuất bằng Phương Pháp in 3D của ASSAB thể hiện những ưu thế rõ rệt, bao gồm:
- Nâng cao chất lượng sản phẩm đúc và giảm tỷ lệ phế phẩm: Khuôn có nhiệt độ phân bổ đồng đều hơn, không có điểm nóng. Các khu vực thành dày của chi tiết đúc được làm mát hiệu quả hơn, giúp cải thiện độ đồng nhất về chất lượng sản phẩm.
- Kéo dài tuổi thọ khuôn: Sự phân bổ ứng suất của khuôn được tối ưu hóa, cải thiện khả năng chống nứt và ngăn ngừa các vấn đề nứt sớm.
- Giảm công tác bảo trì: Giảm thời gian chết và chi phí bảo trì do lỗi khuôn.
Những lợi thế này đã được thể hiện rõ ràng trong thực tế sản xuất đúc . Dưới đây là một số ví dụ ứng dụng thành công giải pháp in 3D của ASSAB:
Trường hợp 1:
Một công ty sản xuất lớn trong ngành đúc gặp phải vấn đề dính nhôm nghiêm trọng tại các lõi khuôn khi sản xuất tủ điều khiển điện tử cho xe sử dụng năng lượng mới. Chất lượng bề mặt của sản phẩm kém, và độ xốp bên trong khiến sản phẩm không vượt qua được bài kiểm tra rò rỉ. Các quy trình sản xuất khuôn truyền thống không thể khắc phục hiệu quả vấn đề này gây ra tình trạng gián đoạn thường xuyên do phải mài thủ công trong quá trình đúc do tỉ lệ phế liệu cao.
Sau khi triển khai giải pháp ASSAB sử dụng lõi khuôn in 3D AM Dievar, việc phải mài sửa thủ công trong mỗi ca sản xuất đã được loại bỏ hoàn toàn, giúp tăng tỷ lệ thành phẩm lên hơn 5% và giảm chi phí sản xuất mỗi sản phẩm lên đến 35%.
Trường hợp 2:
Một nhà cung cấp linh kiện ô tô đã sử dụng các lõi khuôn in 3D với kênh làm mát đồng bộ (conformal cooling) nhằm giảm điểm nóng khi đúc một bộ phận trong hệ thống tuần hoàn khí thải động cơ. Tuy nhiên, các lõi khuôn này bị nứt sau 50.000 đến 60.000 chu kỳ đúc, không đạt được tuổi thọ khuôn như kỳ vọng.
ASSAB tiến hành phân tích khuôn và tối ưu hóa giải pháp kỹ thuật. Bằng cách sử dụng vật liệu AM Dievar để in 3D lõi khuôn, tuổi thọ khuôn đã tăng lên 40-50%. Nhờ đó, chi phí sản xuất mỗi sản phẩm giảm xuống còn 50% so với khi sử dụng lõi khuôn cũ. Tuổi thọ lõi khuôn cũng đáp ứng được yêu cầu cho toàn bộ lô sản xuất.
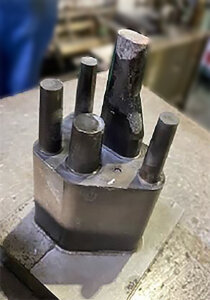
Trường hợp 3:
Một nhà sản xuất trong ngành đúc đang sản xuất linh kiện động cơ với số lượng lớn và yêu cầu chất lượng ổn định. Để rút ngắn thời gian chu kỳ sản xuất, họ đã sử dụng công nghệ in 3D với bột kim loại 1.2709 để chế tạo bộ phân phối, nhằm mục đích nâng cao hiệu quả sản xuất. Tuy nhiên, chỉ sau khoảng 12.000 lần đúc, bộ phân phối bị nứt và không thể sử dụng được nữa.
ASSAB đã tối ưu hóa thiết kế kênh làm mát bằng quy trình thiết kế 5 bước và sản xuất bộ phân phối bằng AM Dievar. Nó đã được đưa vào sản xuất cho hơn 35.000 lần đúc mà không gặp phải bất kỳ sự cố nào. Tính dẫn nhiệt cao xuất sắc của AM Dievar đã dẫn đến những cải thiện hơn nữa về hiệu quả sản xuất so với 1.2709. Các bộ phân phối được in bằng AM Dievar hiện nay đã được các khách hàng ở khu vực Châu Á – Thái Bình Dương xác nhận thành công để sản xuất hàng loạt. Đối với một nhà sản xuất cụ thể, tuổi thọ của các bộ phân phối này đã vượt 200.000 chu kỳ.
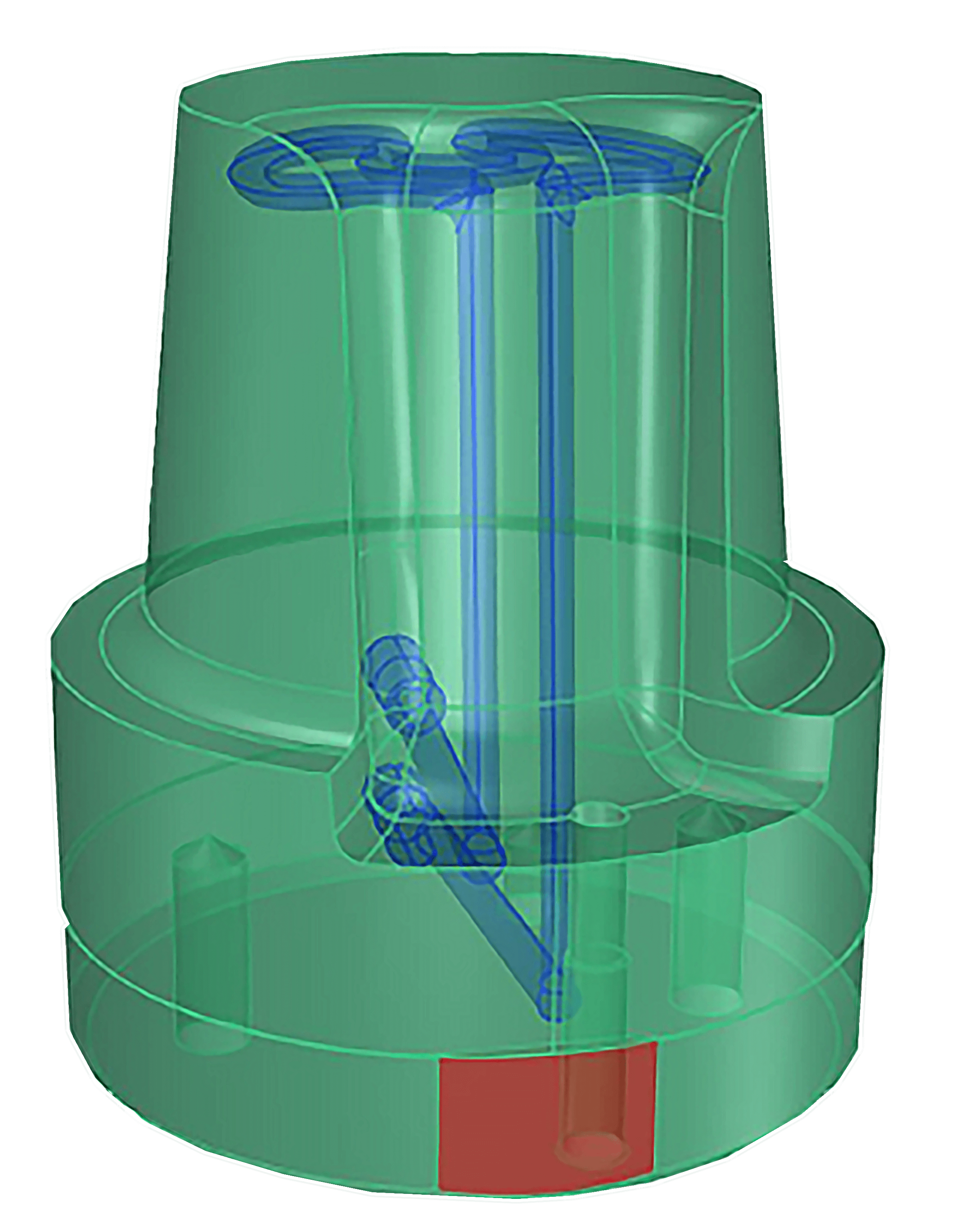
Các trường hợp bên trên chứng minh tiềm năng của các giải pháp in 3D của ASSAB trong việc cải thiện chất lượng sản phẩm và hiệu quả sản xuất, cũng như giảm chi phí sản xuất.
Thêm vào đó, việc ứng dụng sáng tạo công nghệ in 3D có thể thúc đẩy phát triển bền vững và đạt được các mục tiêu về môi trường.
Trong một trường hợp ứng dụng thành công với bộ phân phối đúc, thời gian chu trình sản xuất đã được rút ngắn 10% nhờ công nghệ in 3D của ASSAB, đồng thời giúp giảm 12 tấn lượng khí thải carbon dioxide. Việc áp dụng công nghệ này không chỉ giúp doanh nghiệp duy trì năng lực cạnh tranh mà còn góp phần bảo vệ môi trường.
Tính toán lượng khí thải carbon – Bộ phân phối kim loại nóng chả
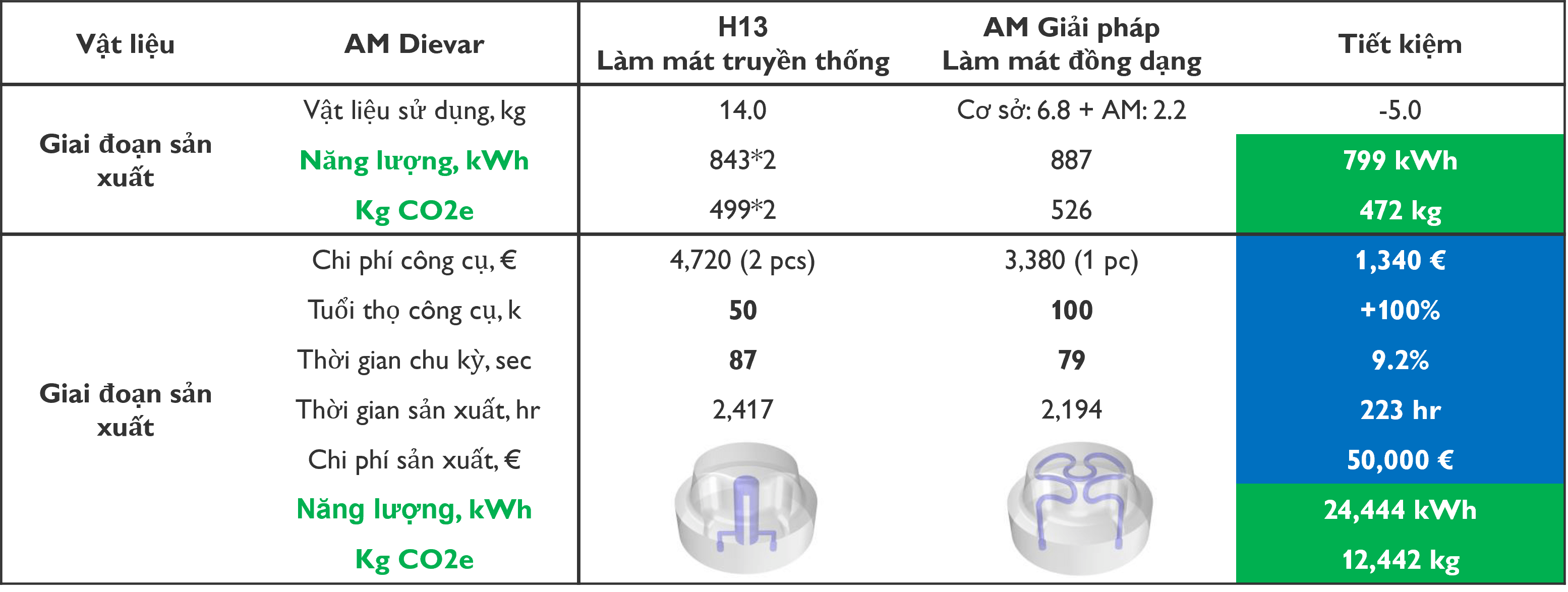
Tài liệu tham khảo
- Mega Die-Casting Brings New Opportunities for Large Die-Casting Mold Manufacturing, http://www.cqmjxh.cn/newsx.asp?id=1372&fid=6&lm=19
- European Aluminium Association Passenger Car Aluminium Usage Study and Forecast Report (2022-2030) – World Aluminium Network
- Revolutionary Die-Casting Technology: Achieving Annual Savings of €45,000 from a €3,000 Investment through 3D Printing